Case studies of Qualica’s introduction
Casting simulation software
JSCAST
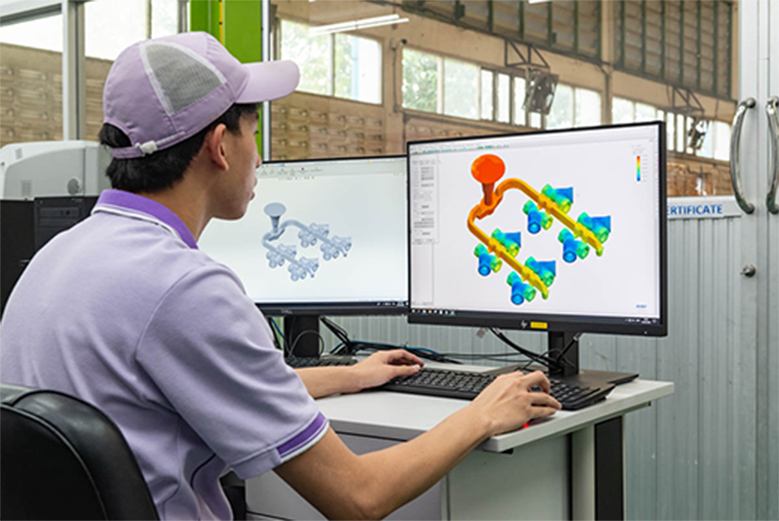
Case studies of Qualica’s introduction
Casting simulation software
JSCAST
Background
Consider installing analysis software for internalized casting molds
Evaluation point
Get firm support
in Thailand
Effectiveness
Accomplish prediction of defects and attempt to improve actively
Background
KITZ (Thailand) Ltd., Thai production base of Japan leading valve manufacturer, KITZ Corporation (HQ: first section of the Tokyo Stock Exchange, Chiba city, Chiba prefecture) is located in Bangplee, Samutprakan province. The location was taken about 1 hour from central of Bangkok towards the east by car. About 1 million each bronze and brass valves are produced a month from casting to integrated production and delivered to countries around the world such as Japan, Asia, and the United States. It has an important role as a production base for products in KITZ Group.
The company had started operation in 1988, while technical department was established in 2017. Until then, the company, as a mass production factory, has pursued production of specified products with high quality and efficiency. However, to further expand market share, it is required product development that flexibly meet local needs. Therefore, setting up technical department in Thailand is for genuine technology accumulation. Noboru Hotta, the first technical officer being assigned to Thailand in 2014, was the key role.
After the establishment, it was challenged by internalizing mold production that has been outsourced. Mold is important element in valve manufacturing and packed with variety know-how.
Thus, if the mold can be in-house manufacturing, the delivery time which could have taken several months, can be dramatically shortened and easier to respond to detailed specification changes. Nevertheless, there was not any know-how in Thailand at all. In the beginning, machines and tools were prepared by imitating what were seen, and the quality has been gradually improved through trial and error. First, when mold manufacturing gets on the right track, it was challenged to manufacture the sand mold used for casting. At the same time, we decided to implement software that analyzes flows and solid process of casting water to plan further technical establishment.
Selection
When implementing analysis software, how operating Thai people actually use was concerned. This is because of the wish that Thai people could take the initiative in technological development in the future.
Thai staff had picked some analysis software, and let software company staff to come to factory for explanation. However, even if there are sales staffs, there was some faults when foreign staff using English for detailed technical support. When exchanging technical information; casting, supporting in Thai language is expected for Thai staff to understand easily.“ we have known that we are amateurs, so supporting in Thai is necessary.” said Mr. Hotta.
Meanwhile, when Mr. Hotta asked the Japanese factory for an opinion, the implement of JSCAST, Qualica's three-dimensional hot water flow coagulation system, was considered. Qualica is located in Bangkok and has Japanese residents. Mr. Hotta promptly contacted by himself. In addition to the functionality of JSCAST, the sense of security that we could receive support in both Japanese and Thai was a decisive factor for the implementation. In May 2019, the project started.
Efficiency
Ornut Yodmanee, a young Thai staff, is in charge of the analysis at JSCAST. Having studied metallurgical engineering in university, she was selected to create a drawing with 3D CAD, set various conditions such as metal of material and casting mold material, and try the analysis. Occasionally, defected casting mold will be used to compare with simulation result in order to find out cause.
JSCAST can visualize hot water flow and solidification form inside casting mold, which previously cannot be seen by naked eye. From a scientific point of view, it is now possible to approach casting mold defects that rely on craftsmen’s experience and intuition. Mr. Hotta has also succeeded in predicting a number of defects through simulations using JSCAST. Furthermore, since simulations can be performed in advance, ideas for improvement have positively come out from the manufacturing site without fear of loss when trial fails. JSCAST is also used for working to increase the number of casting molds to improve yield, verifying hot water flows solidification when the number of casting molds increases, changing the shape runner and adjusting casting molds.
"I didn't know there was this sort of software, so I'm enjoying it as new experience. It was difficult at first, but I got used to it little by little, and I'm getting better at using it" says Ornut. Technical support is provided by Thai staffs from Qualica. Since she is fluent in Japanese, she learned by listening to Japanese Qualica employees who are familiar with casting. Mr. Hotta also says "It's really helpful because Thai people can talk technically with each other without me." Another merit of JSCAST is that you can easily create an analysis model in a short time by importing 3D CAD data with a unique interface. "It's easy to understand and use. It has enough functionality" (Mr. Hotta).
Next step of development
Currently, JSCAST is used to reduce defects in casting molds which is mainly used. In Thailand, rubber parts using for valves and aluminum die-casting are also molded. Therefore, there is a plan to simulate all the moldings in Thailand by the engineering department and utilize it for defect verification in the future. Furthermore, if the operation of JSCAST progresses smoothly in Thailand, know-how cultivated in Thailand can be transferred and operate in Japanese factory that is also being considered implementation. Japanese side is also looking forward to further achievements in Thailand.
In the 4th medium-term management plan announced in 2019, KITZ aims to become "Global Strong No. 2" (The second in the world sales ranking) in the valve business toward 2030. Japan, 3 main bases (Europe, America, ASEAN) and two hubs (China, India) have been positioned as priority areas for global market, and will be developed business in response to each market environment. In 2018, we are aiming for top share in Southeast Asia by establishing local subsidiary in Vietnam founding representative office in Indonesia and so on.
Mr. Hotta says with high expectation for the future, "I hope Thai people will be a center to support factory". It will not be long until the day that the products which are designed by Thai staffs from technical department will contribute to expand market share.
Casting simulation software JSCAST
Click here for details.