Case studies of Qualica’s introduction
Support Cloud system
for
manufacturing industry
Production management system
「ATOMS QUBE」
ITAOTEC(THAILAND)CO., LTD.
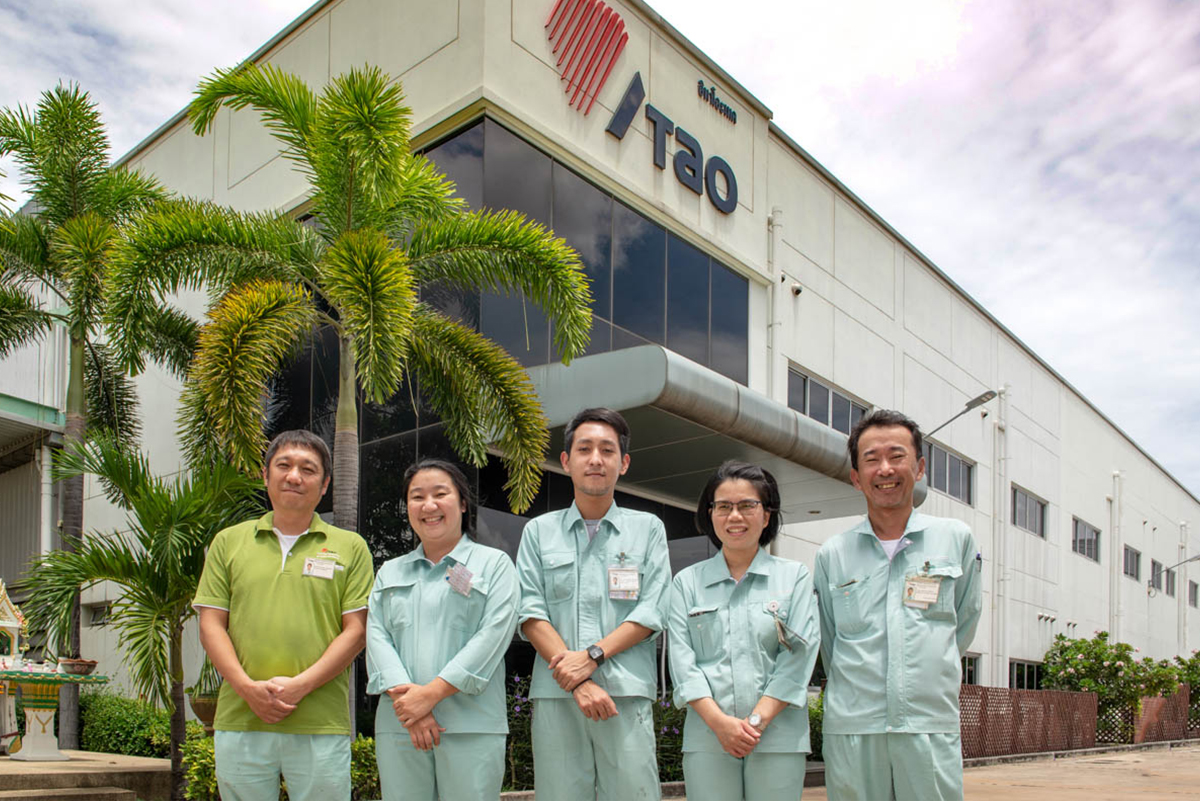
Case studies of Qualica’s introduction
Support Cloud system
for
manufacturing industry
Production management system
「ATOMS QUBE」
ITAOTEC(THAILAND)CO., LTD.
Background
Limits of appearing Excel management
Introduction
Unify consciousness between Thai and Japan for decisive factor
Effect
Formulate production plan without time loss
Background
Founded in 1951, ITAO iron works set its headquarters in Komatsu city, Ishikawa prefecture and mainly manufactured parts for construction and industrial machinery. Supplying to world’s leading Komatsu and Caterpillar. Currently, there are four factories in Ishikawa prefecture. ITAOTEC (THAILAND) is the only overseas factory, located in Pinthong industrial park in Sriracha, Chonburi province. Like in Japan, we manufacture idler cushion assemblies and work machine pins, which are undercarriage parts for construction machinery, from machining to heat treatment, welding, and assembly, and supply them to Komatsu in Thailand, Indonesia, and India.
In 2009, when first operation was started, factory’s size was only about a quarter of current 4,000 squares meter factory and parts were all imported from Japan and did only assembly. From there, industrial machinery, welding machines and quenching equipment were introduced gradually to increase the range of works and develop it into current integrated production system. Meanwhile, the issue was the production management which operated by Excel from the establishment. Even if there were not many items to handle, as the business expands and the number of items handled and customers increases, the daily Excel input work has become enormous.
Because of the numbers that came up from each site are input manually, mistaken typing may occur. Furthermore, files exist for each person in charge and departments apart from production management such as sales and accounting, therefore, it was difficult to share information when sudden order changes occur. Although the work has proceeded smoothly by the efforts of Thai production management leader, Pornthip Aryuyuen, the dependence is high. Therefore, there is constant concern if something happens to her. Is it all right as it is? Therefore, the introduction of a production management system was started to consider in earnest.
Introduction
As a result of asking surrounding companies, Qualica's cloud support production management system "ATOMS QUBE" was selected as a candidate. It is equipped with all the functions required for production management, such as order shipping, purchasing, inventory management, and production planning, and because it is a cloud type, it can be installed immediately with a personal computer connected to the Internet.
However, system introduction will be certain amount of investment. The discussions, whether it was really necessary, were held between Thai corporation and the Japanese headquarters. Japanese staff of Qualica's Thai also went to the headquarters in Komatsu City to explain in detail. There was a time when a production management executive from Japan visited ITAOTEC on a business trip, he said "Everyone is working by looking only at the Excel screen. It would be good if we could reduce this burden as much as possible so that we could do other work. "4 out of 5 persons in production management departments were busy with input work. Eventually, Japanese headquarters, Thai corporation, and above all, Thai staff at the site were united toward the introduction.
The project was kicked off in May, 2019. There were several meetings between Qualica and ITAOTEC that took several hours each time, basically twice a week over two months period. The discussion on how to replace works that were done in Excel with the system was continued. Then, "Atoms Qube" started to operate in earnest, by the end of the same year.
Effectiveness
Since the numbers that were input in each department are immediately reflected in the system after operation, the input work of production management department dramatically decreased. Then, information sharing has greatly progressed. Pornthip said “Previously, each department often questioned me how much is in the stock. Now, anyone can get into the system, they no longer have to come for asking.
As the number of simple input work has decreased, time for checking whether the numbers are correct has increased. Just looking at the system will be able to immediately figure out data that has not been input in process yet. Production management system has also been installed at the head office in Japan, so it has become easier for business travellers from Japan to figure out actual situation in Thailand compared to complicated Excel management.
The fact that information is reflected on by one lead to production planning based on more real-time data. When using Excel management, sometimes it took a whole day from ordering time until transmitting to production management, causing a time lag. Currently, once your order is registered in the morning, production plan can be made within the same day.
After installing the system, Yuji Nishino, the factory manager, also felt the change in the site. "When I was working by Excel, I sometimes felt that there was too much stock on the site, or conversely too little. Currently, stocks seem to be stable. Naofumi Tatsumi, the production manager who led the introduction at that time, responded, "Production management is the job of delivering goods to the manufacturing site and transporting finished goods from the site to the next process. I am happy to hear that goods flow smoothly.
Also, the order registration work has been simplified. In case of big company, the order until next year may be input in the form of unofficial schedule. However, weekly changes will come about after all. In the past the person in charge had to add changes to Excel each time, but with the introduction of the system, "it can now be pasted as it is as data" (Mr. Tatsumi).
The next development
Shortly after starting to use "ATOMS QUBE" in earnest, Pornthip said "To be honest, it’s not 100% proficient. We are still learning. And the more we know the higher we demand.” The search for what and how much can be done is continuing. Now that we have a system that able to share information, the focus is changing to how to utilize that information as the next step.
Pornthip said “I want everybody to understand the system in the same level. That way, even if someone is missing, the hole can be filled immediately. Based on shared data, each department will independently decide what to do. Changes in the awareness of each staff are expected.
Last year, ITAOTEC celebrated 10 years anniversary, since the factory started the operation. Mr. Yusei Kitamura, as president who leads the company on his second assignment, said "It was very pleasant to see how the company has grown little by little over the last 10 years." Aiming for further development, Japanese and Thai staff will continue working hard together.
Cloud-enabled production management
Click here for details.